The Ultimate Guide to Welding WPS Procedures: An Extensive Introduction for Welders
In the complex world of welding, Welding Procedure Specifications (WPS) function as the foundation of guaranteeing quality, consistency, and security in welding procedures. Understanding the subtleties of creating, implementing, and monitoring WPS procedures is vital for welders looking to elevate their craft and satisfy sector requirements. As we look into the different parts of a WPS and check out the details of credentials and accreditation, we will certainly uncover the essential function these procedures play in the world of welding. Let's get started on a journey to unravel the intricacies and value of WPS procedures in welding practices.
Relevance of WPS Procedures
Recognizing the relevance of Welding Procedure Requirements (WPS) treatments is critical for making sure the quality and stability of bonded structures. WPS treatments function as a roadmap for welders, detailing the needed steps, specifications, and materials required to attain a sound weld. By adhering to WPS guidelines, welders can make sure uniformity in their work, causing structurally audio and dependable welds.
One of the key reasons why WPS procedures are necessary is their function in keeping weld quality and honesty. Adhering to the defined welding criteria and techniques outlined in the WPS aids prevent issues such as porosity, cracking, or insufficient fusion, which can endanger the toughness and longevity of the weld.
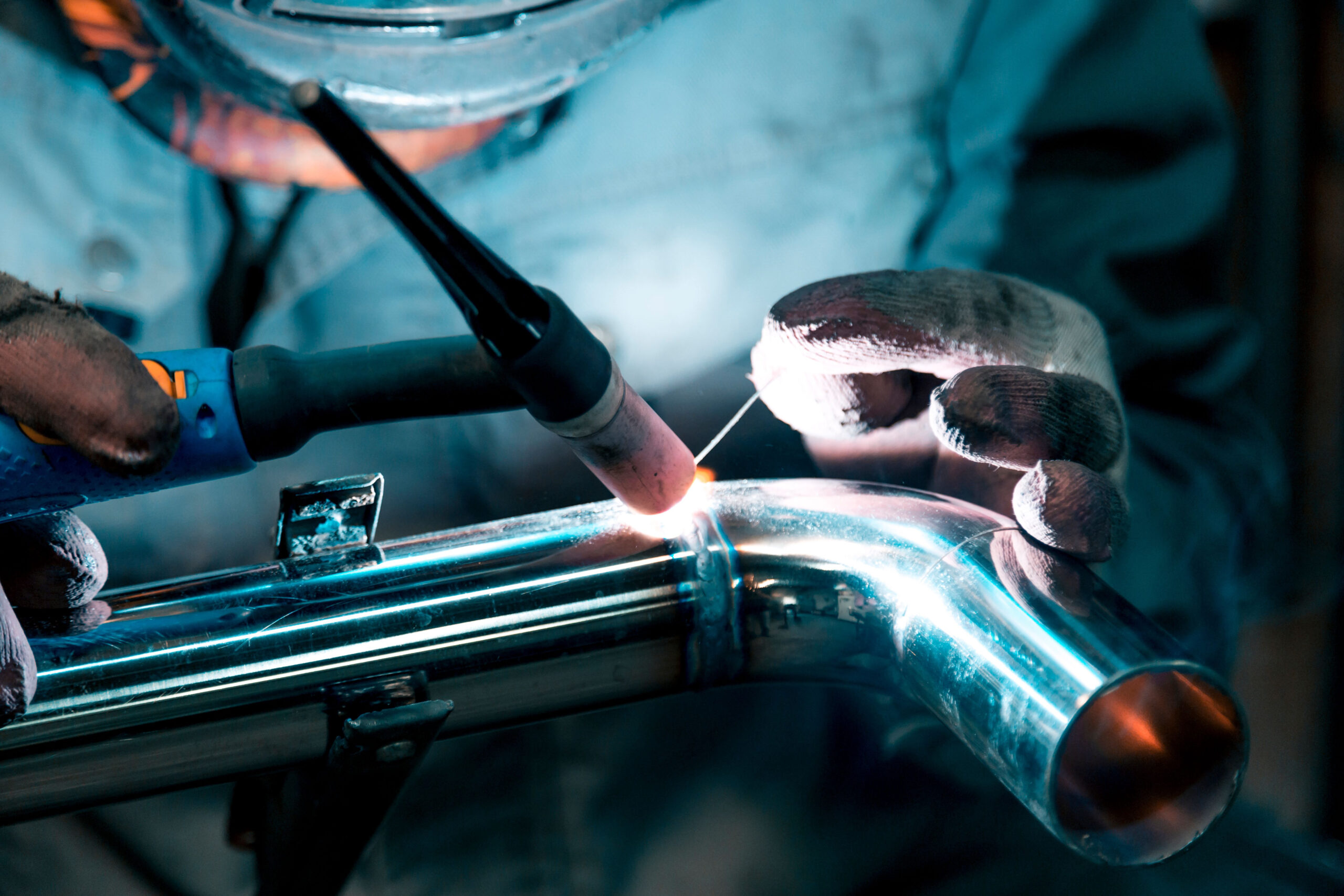
Elements of a WPS
A Welding Procedure Spec (WPS) typically comprises vital parts that information the specific needs for performing a weld, ensuring consistency and top quality in the welding procedure. The key elements of a WPS include crucial variables such as base metals, filler metals, preheat and interpass temperatures, welding processes, shielding gases, welding placements, and post-weld warmth treatment demands.
Base metals refer to the products being signed up with, while filler steels are used to load the void between the base metals during welding. The welding process lays out the certain method to be made use of, whether it's gas steel arc welding (GMAW), protected metal arc welding (SMAW), or one more method. Welding positions define the alignments in which welding can be carried out.

Certification and Certification
Having actually developed the necessary parts of a Welding Treatment Requirements (WPS), the focus now changes in the direction of the critical aspects of qualification and accreditation in welding methods.

Certification, on the various other hand, is the official recognition of a welder's credentials by a relevant qualification body or organization. Welding certifications are usually based upon the details welding processes, products, and positions a welder is qualified to collaborate with. Holding a legitimate read here welding qualification shows that a welder meets industry criteria and is experienced to do welding jobs to the needed requirements.
Producing a WPS
To create a Welding Procedure Spec (WPS) that fulfills market standards, careful consideration of welding procedures, products, and operational specifications is vital. The first step in creating a WPS is to determine the welding process to be used, such as gas steel arc welding (GMAW) or shielded metal arc welding (SMAW)

Implementing and Keeping Track Of WPS
Upon completing the comprehensive Welding Treatment Spec (WPS) that carefully details welding processes, materials, operational parameters, and top quality guarantee actions, the focus shifts to efficiently implementing and monitoring the recognized procedures. Implementation includes making certain that all welders entailed in the project are familiar with the WPS and follow it thoroughly throughout the welding procedure. Efficient implementation and surveillance of the WPS are crucial for guaranteeing the integrity, stamina, and safety of the welded joints, inevitably adding to the total success of the welding job.
Conclusion
In final thought, understanding and complying with Welding Procedure Requirements (WPS) is important for welders to make sure top quality, consistency, and safety in their work. By knowing the parts of a WPS, obtaining appropriate qualifications and qualifications, producing comprehensive treatments, and implementing and monitoring them efficiently, welders can improve their abilities and effectiveness in welding practices. Sticking to WPS procedures is necessary try this web-site for producing top quality welds and conference industry criteria.
In the intricate world of welding, Welding Treatment Specifications (WPS) offer as the backbone of making certain quality, uniformity, and security in welding procedures. The welding process describes the details technique to be utilized, whether it's gas steel arc welding (GMAW), secured steel arc welding (SMAW), or another technique.To develop a Welding Procedure Spec (WPS) that fulfills industry requirements, cautious factor to consider of welding procedures, materials, and functional parameters is important. The very first step in producing a WPS is to recognize the welding process to be made use find of, such as gas steel arc welding (GMAW) or shielded steel arc welding (SMAW)Upon finalizing the detailed Welding Procedure Specification (WPS) that diligently information welding procedures, materials, functional criteria, and high quality guarantee actions, the focus moves to efficiently carrying out and keeping an eye on the well established procedures.